
Case Studies
The latest case studies from SCT
The Situation
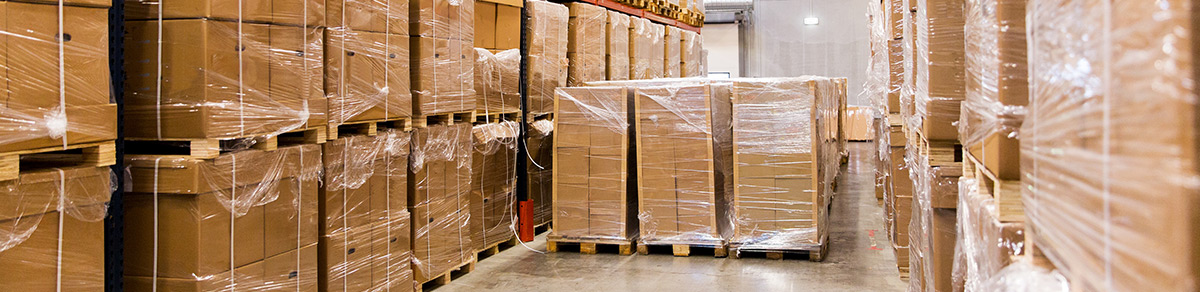
The company’s outbound logistics operation was highly dependent on many manual steps, in both the picking and packing process, causing operational inefficiencies, poor performance and elevated packaging, shipping and labor costs.
For even the most skilled warehouse employee, identifying the right packing configuration in real-time, every time, can be difficult. Any errors at this stage slow down and disrupt overall warehouse processes. Trying to accomplish pick and pack optimization, manually, became more challenging for the facility during peak seasons, when the operation relies on seasonal or temporary employees who were not proficient in optimal packing strategies.
Both seasoned and new employees had challenges in terms of selecting the right box, and using the optimal packing configuration the first time every time. These suboptimal packing configurations resulted in costly repacking efforts that reduced productivity and introduced unnecessary labor costs. These manual processes also introduced risk due to the potential of incompatible products getting packed and shipped in the same container.
In addition to its negative impact on productivity and efficiency, the manual pick/pack process also resulted in direct financial costs from unnecessary containers, boxes and dunnage. Even more significant was the negative impact on shipping costs—particularly in the wake of dimensional weight pricing.
With a host of variables to consider, from material incompatibilities, to overpack considerations, fragility requirements and item orientation, optimizing the pick and pack process is more complicated than ever. In an intensely competitive industry, the company’s warehouse processes were inhibiting its ability to compete.
The Solution
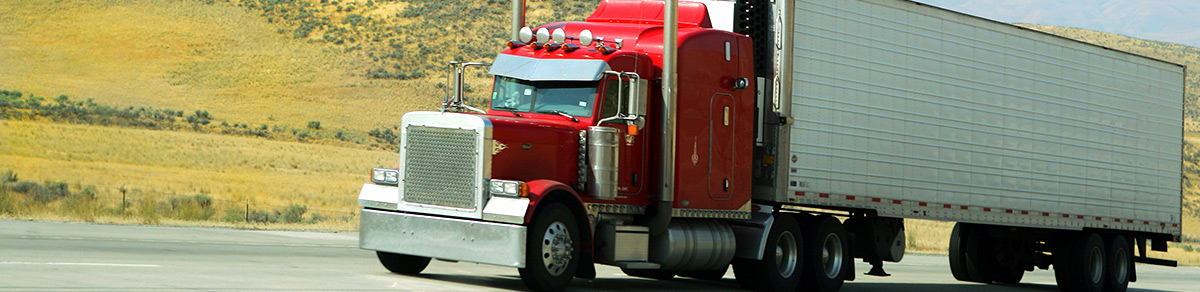
In an effort to alleviate the burden on warehouse staff, dramatically improve process efficiency and reduce shipping costs, the company implemented SCT’s Carton Space Optimizer (CSO)— pack planning software that eliminates guesswork and systematically considers the many variables that impact packing optimization.
With its newly adopted packing software, the company was able to eliminate the negative impact of inconsistent tribal knowledge across shifts, and mitigate its reliance on a few skilled and tenured team members. By implementing CSO, the company has optimized its pick to shipping container process while adhering to all relevant business rules and compliance guidelines and identifying the best packing configuration for every shipment. Overall, the company has improved its entire pick to shipping container process, almost eliminated the need for repacking, and is experiencing a significant throughput increase.
The company also implemented CSO’s 3D visualizer. This innovative tool provides intuitive visual depictions of the optimized packing scenario. This provides efficient feedback on complex packing proposals, improves packing performance and reduces training time for new, temporary or seasonal employees.
The company has significant shipping volume and complexity, which means business rule adherence is vitally important. Since CSO is built in SAP it easily takes these rules into account before determining the optimal pack. This allows it to automatically address customer-specific packing requirements, consider weight restrictions, reduced the risk of product incompatibilities within shipments and ensure the appropriate space is left for protective dunnage including cold packs and dry ice. CSO also ensures adherence to DG per carton maximum quantity restrictions, including lithium batteries and other limited quantity shipping items. Customer or internally-defined packing rules may also be incorporated.
By implementing SCT’s Carton Space Optimizer (CSO) the company improved its packing and shipping operation by ensuring the right box is selected for its pick-to shipping container process—reducing double handling and repack, improving fill rates, reducing the number of packages shipped, reducing dunnage consumption, ensuring business rule adherence and reducing the overall freight spend.
Discover CSO
CSO delivers the most accurate packing proposal through an algorithm that considers volume, dimension and multi-axis orientation of products within the shipping container. We call this comprehensive approach the dynamic fill method. Companies that implement SCT’s advanced packing software, built in SAP, can achieve significant year-over-year savings by consistently leveraging the lowest freight cost packing proposal, driven by their business rules, while optimizing their pick and pack process
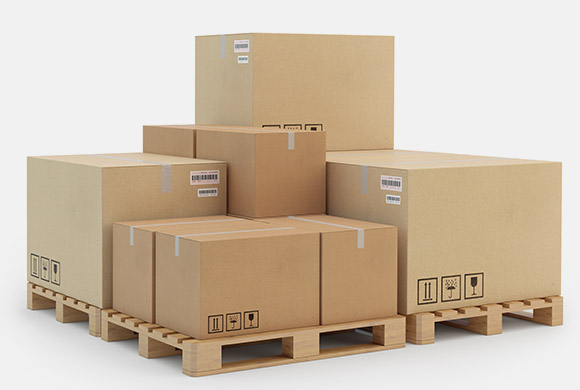